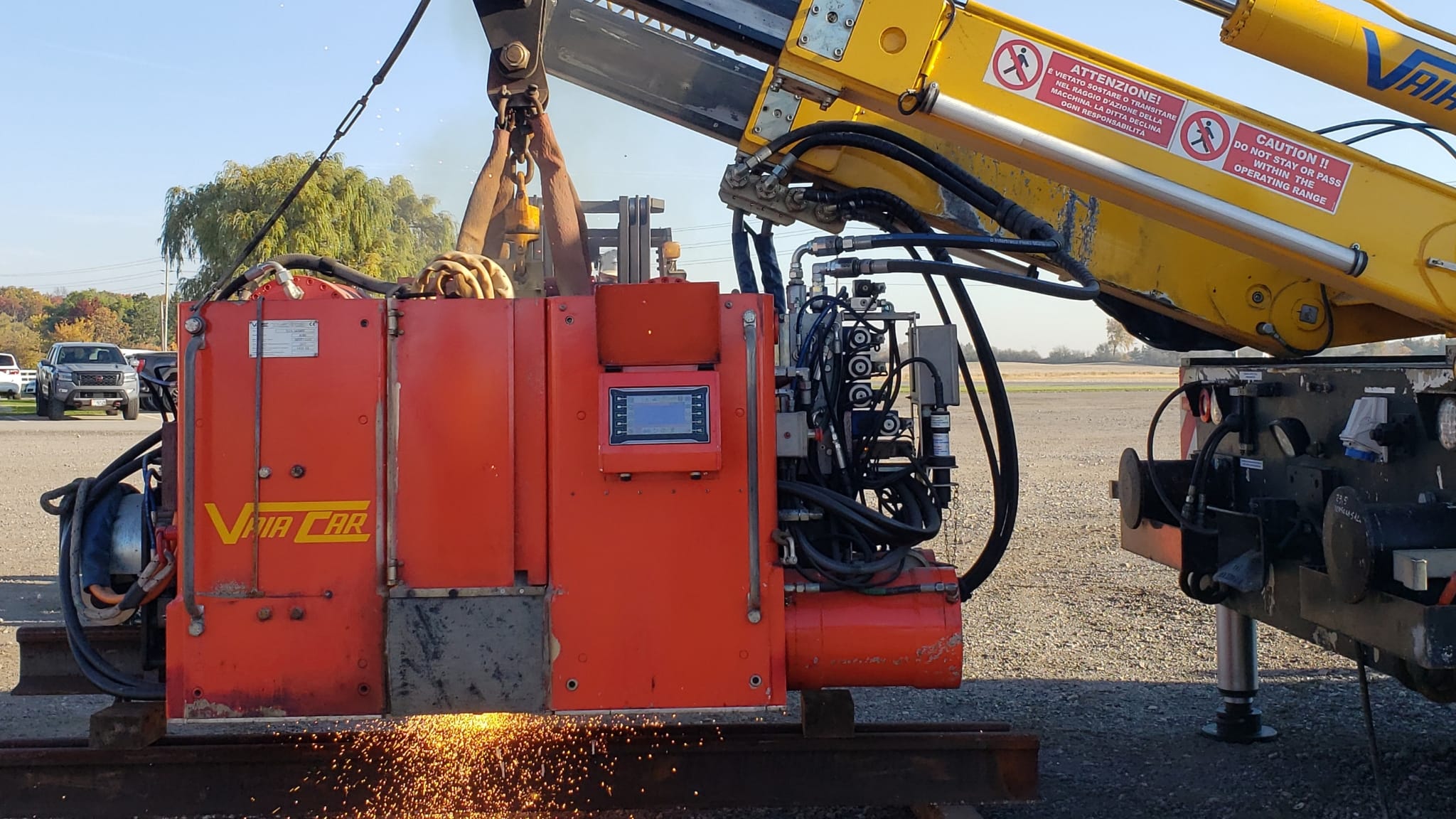
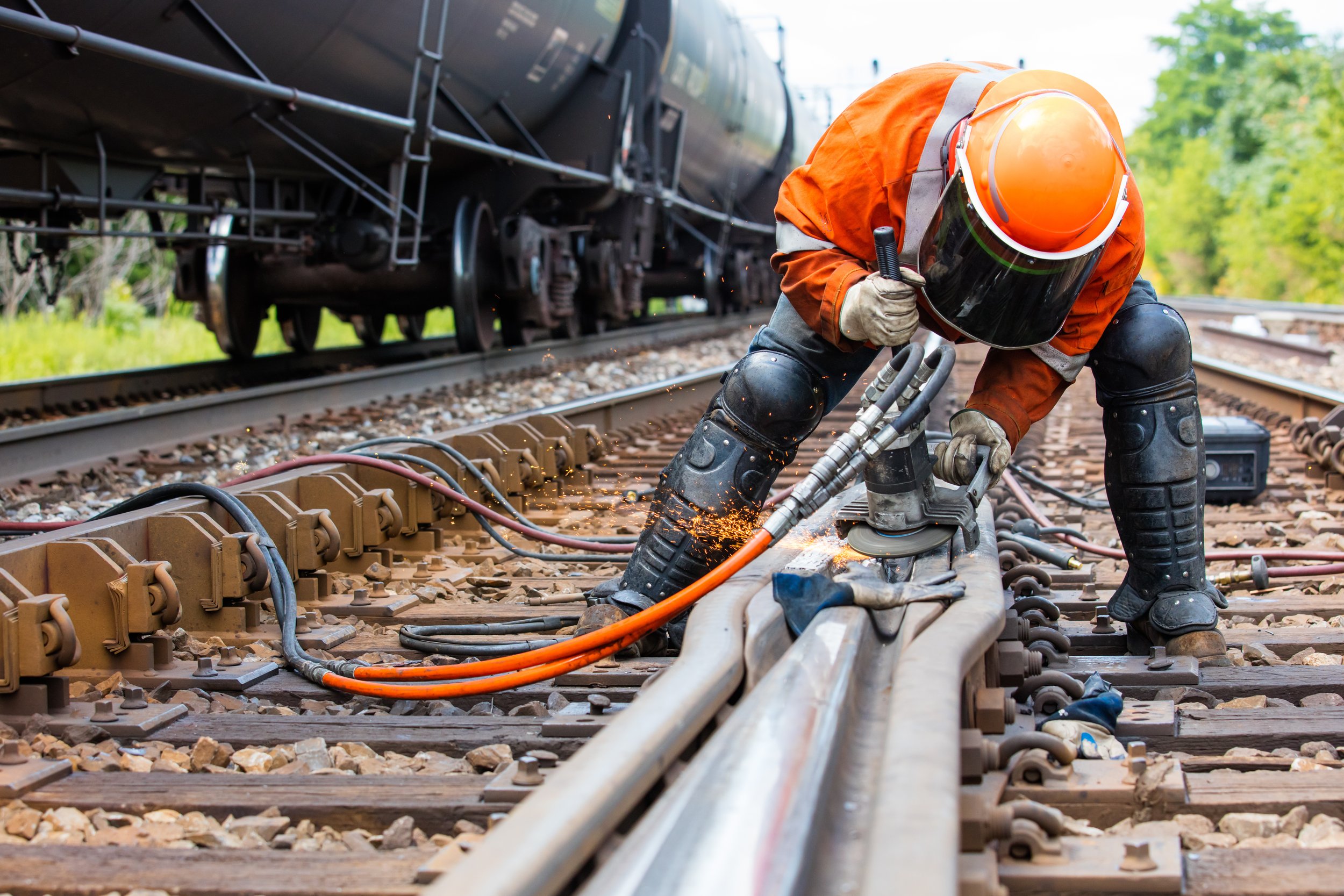
Flash butt welding
Flash butt welding is a specialized technique predominantly utilized in rail welding plants. This method involves welding small parts together through high-voltage resistance, where components are aligned end-to-end and fused using high current density. During the welding process, long gauge rails, typically around 100 meters, are placed in a dedicated machine and heated based on the thermal effects of the current. Once the rail reaches a plastic state, it is rapidly extruded, ensuring a robust joint. The primary advantage of flash butt welding is that it creates a bond with a strength equivalent to that of the base metal, resulting in a smooth surface that can be easily polished. However, its application is limited to factory settings, making it less versatile for on-site welding.
- Utilizes high-voltage resistance to fuse components end-to-end with high current density.
- Produces strong welds equivalent to the base metal strength, ideal for long gauge rails.
Thermite welding
Alumino-thermic welding, commonly known as thermit welding, utilizes the heat generated from an exothermic reaction to achieve coalescence between metals. The term “thermite” refers to the reaction involving metal oxides and reducing agents, where a mixture of low-formation heat metal oxides and high-formation heat metallic reducing agents creates a significant amount of heat during oxidation. This heat is harnessed to melt and fuse the two rail sections together. Suitable for outdoor construction sites, this method involves a redox reaction between iron and aluminum, producing molten iron that effectively welds the rails. Compared to flash butt welding, thermit welding is faster and offers stable quality; however, it requires a larger initial investment in equipment and substantial power. While pneumatic welding has lower upfront costs and shorter welding times, it has strict requirements for joint preparation and can be challenging for ultra-long rails or continuous track sections. Overall, thermit welding is relatively simple and requires less operator expertise, but its welding quality may not match that of contact or gas pressure welding.
- Relies on an exothermic reaction between metal oxides and aluminum to generate heat for welding.
- Suitable for outdoor applications, offering faster welding speeds and stable quality.
Working Process
We are proud to have our Occupational Health and Safety Management System CORTM Certified.
categories
Let’s Start Work Together
851 Haldimand, Hwy#56 RR#1
York, ON N0A 1R0